section epub:type=”chapter” role=”doc-chapter”> Matthew D. Barnhart There are now many different locking plate systems available to veterinarians. While they differ from each other in a variety of ways, the majority have in common the fact that they are fixed‐angle locking systems. Screwhead and plate threads are machined precisely such that the screws must be inserted into the plate at a predetermined angle in order to achieve a locked coupling. Failure of precise placement can result in compromised screw locking and/or cross threading between the plate hole and screwhead threads, causing incomplete insertion and challenging screw removal. The fixed angle also limits flexibility for screw placement when there is a need to avoid joints, fracture lines, and other implants. Additionally, some fracture locations (e.g. acetabulum) can be difficult to insert drill guides at 90° to the bone because of regional anatomic constraints. By contrast, only two multidirectional locking systems, which offer freedom from fixed‐angle insertion requirements, have been reported in the veterinary literature [1, 2]. In 2009, the Polyaxial (PAX) Advanced Locking System was introduced into the veterinary market in order to provide the benefits of locking plate technology with a unique multidirectional angle stable (i.e. polyaxial) screw insertion option. The PAX screws are made of a titanium alloy that is approximately twice the hardness of the titanium PAX plate. Locking coupling is achieved by structural deformation of the vertical plate hole ridges by the sharp, cutting threads of the harder screwhead that occurs during tightening. PAX screws can be inserted multidirectionally up to 5° within the plate without a significant loss of push‐out strength. At an insertion angle of 10° the push‐out strength does decrease significantly; however, it is still higher than the pullout strength of 3.5 mm cortical screws in bone [3] (Figure 10.1). While successful screw‐plate coupling can still occur at insertion angles in excess of 10°, push‐out strength progressively decreases. Using the PAX drill guide helps to prevent drilling at an excessive angle as it will fulcrum out of the plate hole if placed at an angle of greater than 15°. Figure 10.1 Illustration of multidirectional stability of polyaxial (PAX) screw within plate. Generating adequate torque is particularly important when inserting PAX screws in order to achieve complete coupling. The greater the depth of screwhead engagement, the more resistance to screw push‐out is generated. A minimum insertion torque of 2.5 Nm has been recommended, with 3.5 Nm being ideal [3–5]. The author recommends using a large‐handled driver for the 2.7 and 3.5 mm screws in order to maximize hand‐generated torque and ensure adequate depth of insertion (Figure 10.2). Screwheads should appear flush to slightly countersunk within the plate when properly inserted. Fortunately, there’s little danger of applying too much torque since the screwheads have the same ability to “cut” their way out as they do in (i.e. no cold welding).
10
The Polyaxial (PAX) Advanced Locking System
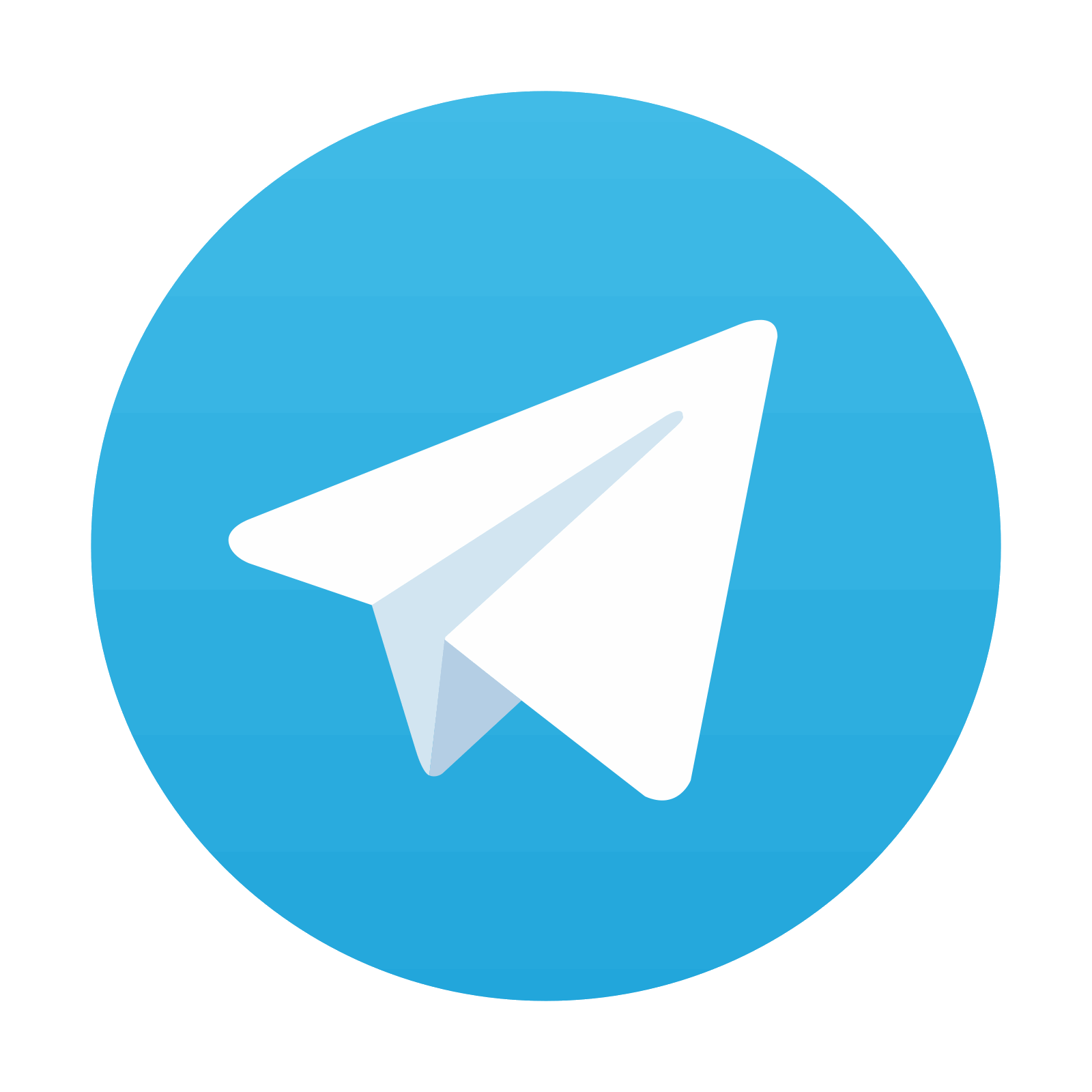
Stay updated, free articles. Join our Telegram channel
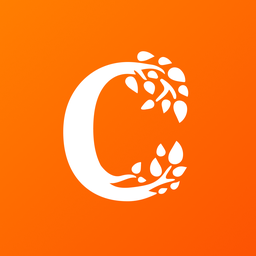
Full access? Get Clinical Tree
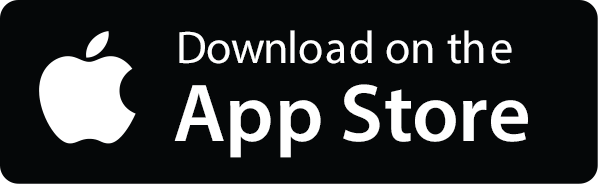
