Al Hollister Gamebird nutrition and feeding is a multistep process that involves not only the determination of the nutrients required for the birds to grow and reproduce, but also the selecting of feed ingredients from those available of adequate quality to meet those requirements, processing as needed and presenting the final feed in a form that will be consumed – all at an acceptable cost. The nutritionist also must consider nonnutritional inclusions in the feed to retain quality, improve palatability, maximize digestibility, and protect the birds from disease and parasites. Feed is often the most expensive part of any gamebird operation, amounting to 50% or more of the total cost of production. It is made up of many ingredients and processes which must be carefully monitored, since small differences often can contribute to large changes in the performance of the birds. Total variables that the nutritionist needs to be aware of include 13 vitamins, at least nine macro‐ and microminerals, up to 20 amino acids, and the numerous ingredients that provide protein, carbohydrates, fats, fiber, and water (the most important, but often overlooked nutrient), plus up to 10 nonnutritional ingredients. Even with the use of premixes for vitamins and trace minerals, there can be as many as 25 different ingredients to monitor in a typical feed. This chapter will briefly describe nutritional and nonnutritional ingredients, processing, presentation, quality control, testing (ingredients and finished feed), feed formulation based on age and species, and the symptoms, diagnosis, and troubleshooting of nutritional problems. Although birds in this group (Galliformes) are often considered primarily seed eaters, they are actually omnivorous, especially as young chicks. With limited gut capacity, and in order to get the concentrated high‐protein and high‐energy diet they need for rapid growth, it is necessary to consume animal protein (insects, worms, small mammals, or reptiles) that are nutrient‐dense foods high in protein and fat while low in fiber. The high water content of these creatures also reduces the amount of drinking water needed. Using protein as an example, live common insects are about 20–25% protein and 60–80% water. If we convert that to 10% water like most prepared feed ingredients, crickets, grasshoppers, and earthworms average 50–60% protein. Grains and seeds are on average somewhat less protein dense but contain more energy (starch and oil). Corn (maize), wheat, milo (sorghum), grass seeds, and many plant buds range from about 7% to 18% protein (again dried to 10% water). Whole soybeans (unprocessed) are an exceptional plant protein source in that they are about 30% protein and 20% fat, and after fat extraction they are 46–48% protein. These plant sources have an amino acid balance that is not complete and must be supplemented, whereas the amino acid balance in animal protein is very close to estimated requirements. To mimic the ration of the free‐living gamebird, it would be appropriate to include some animal protein in formulated feed to provide the necessary amino acids. However, it is possible to duplicate that amino acid profile with plant‐based materials when necessary. The nutrient requirements of game birds have not been well researched. Most of the published data is based on chicken and turkey research [1, 2]. The research with chickens and turkeys, as well as the small amount done with gamebirds, was done under the low‐stress, nearly ideal conditions in research facilities. Therefore, the information presented in Table 7.1 on suggested nutrient levels is based not on minimal nutrient levels under research conditions, but on the common industry practice of utilizing overages of some nutrients to compensate for unknown requirements and losses of nutrients during processing and storage, plus experience under actual field conditions. Table 7.1 is not meant to be all‐inclusive and should be considered only a basis or minimum for formulators or those troubleshooting a suspected nutrition‐related problem. Due to limited space, only the amino acids likely to be limiting in a corn‐soybean diet are included. Formulas made up of other ingredients will need to consider the other essential amino acids. Nutritionists will find it necessary to make additional adjustments based on species, strain, age, management, the rearing environment, and feed storage conditions. Table 7.1 is designed for birds in three general groups: (i) birds that are to be released; (ii) birds that are of the same species but raised for meat production; and (iii) birds that do not require the higher protein (more nutrient‐dense) diet. The sequence of diets for each group is identified with numbers referring to diet crude protein and metabolizable energy (ME); for example, 28 : 1250 is a feed containing 28% protein and ME of 1250 kcal/lb. Table 7.1 Suggested nutrientsa) for pheasants, partridge, bobwhite quail, wild turkey (Group 1), meat birds (Group 2) or guineafowl, coturnix quail and mallard ducks (Group 3). a) The amounts represent as‐fed. Assume 90% dry matter. See the text for diet selection procedure for Groups 1, 2, or 3. b) Amino acids: only those most likely to be limiting in corn‐soy diet are included. c) Grower or finisher refers to strains raised for meat or flying (strains for release). d) Maintenance range: higher energy may be required in colder climate conditions. e) Breeder (small) refers to smaller, more active strains. f) Breeder calcium: use 1.5% for breeds with small clutches (peafowl, etc.). Group 1 is gamebirds that would be released and includes ring‐necked pheasants, partridge, bobwhite quail or wild turkeys and the sequence would be 28 : 1250 starter >20 : 1250 grower >18 : 1200 flyer >14 : 1150 maintenance >18 : 1273 breeder. Under cold climate conditions, a switch to 1250 ME maintenance may be necessary. Smaller, more active strains could use alternate 24 : 1300 breeder. Group 2 are the same birds as Group 1 but used for meat production and would use the numbers in parentheses in the table as follows: 28 : 1250 starter >22 : 1318 grower >20 : 1350 finisher. Group 3 birds are the coturnix (Japanese) quail, guineafowl, and wild‐type mallard ducks and would use 24 : 1250 starter #2 > 20 : 1250 grower >16 : 1250 maintenance >18 or 20 : 1273 breeder. Peafowl or species of pheasants, partridge, and quail not used for release or meat would use the Group 1 sequence to prevent excess body fat and use an alternate breeder diet containing only 1.5% calcium to prevent articular gout. For those preferring metric numbering, remember to multiply the kcal/lb. or mg/lb by 2.2 to get kcal/kg or mg/kg (ppm). Most basic poultry and gamebird diets can be formulated with the relatively small numbers of ingredient types. This would include carbohydrate from grains like corn (maize), wheat, or milo (sorghum), protein from soybean meal, canola or corn gluten meal, animal (meat meal, fish), plus calcium carbonate, dicalcium phosphate, salt, vitamin‐mineral premix, methionine, lysine, and fat. For birds that need to be kept lean and athletic for release, additional low‐energy ingredients (wheat middlings or alfalfa) may be necessary to provide less nutrient‐dense formulations and will be discussed later in this chapter. Finally, nonnutritional feed additives like pellet binders, mold inhibitors, mycotoxin binders, antibiotics, coccidiostats, probiotics, enzymes, and wormers may be required. To accurately formulate a diet, the nutritionist must know the specifications of each ingredient. For grains and protein sources, this would include crude protein, fat, ME, moisture, amino acid profile, crude fiber, calcium and phosphorus – at the very minimum. Averages of these numbers are often obtained from research with ingredients that are assumed to be of uniform quality (i.e., most corn is US #2), and are reported in publications like NRC Poultry (1994) or the Feedstuffs Reference Issue and Nutrition Guide. However, these specifications should be considered only a guide because crops change from year to year and by region grown, and should be verified with test results. Due to space limitations, only the more common ingredients will be covered in this presentation. Corn is the most widely used energy source for all kinds of livestock. It is highly digestible for gamebirds and does not contain antinutritive factors. Although the amino acid profile is not ideal, this can be easily resolved through the use of a good protein source like soybean meal and small additions of amino acids, like methionine and lysine. Standards for grading corn and other grains are provided for and defined in the Official United States Standards for Grain, US Department of Agriculture (USDA) Agricultural Marketing Service, Grain Division. This includes information on minimum pounds per bushel (one bushel = 2150.42 cu in.), maximum percentages of moisture, broken kernels, foreign materials, and damaged kernels. US grade #2 corn must be a minimum of 54 pounds per bushel, 15.5% or less moisture, 3% or less broken kernels and foreign material, and less than 5% damaged kernels. Similar guides are provided for wheat and other grains (includes soybeans). The disadvantages to the use of corn (high levels) include poor pellet quality and the potential for mold or mycotoxin contamination in some locations (weather‐related stress) or if it is not stored properly. Soybeans are an excellent source of vegetable protein and have an amino acid profile that works well in combination with corn. Usually, only methionine is needed to complete the amino acid profile (and sometimes lysine). Soybeans are normally available in a whole, roasted form averaging 38% protein and 18% fat, or as dehulled and solvent processed soybean meal which is usually 46–47% protein and 2% fat. Like corn, detailed standards for grading soybeans are provided by the Official United States Standards for Grain. Disadvantages can result from poor processing; if not enough heat is used, antinutrients (like trypsin inhibitors) are not destroyed, while overheating may result in reduced availability of the important amino acid lysine. Soybean meal also contains nonstarch polysaccharides (NSP) which are hard for young birds to digest. It is recommended that an enzyme be used in high‐protein starter diets, especially those without other nonsoybean protein sources (meat meal, fish meal, corn gluten meal, etc.); this will be discussed later with enzymes. Wheat is commonly used primarily for flour production for human consumption, but if wheat is available at a reasonable price and corn is unavailable or too costly, it can replace corn in gamebird diets. To prevent problems with excessive viscosity that causes poor digestibility and wet manure, the addition of an enzyme (xylanase) is necessary when using high levels of wheat. The byproducts of flour production, like wheat middlings, retain small amounts of starch, making them excellent pellet binders. In addition, the low energy resulting from starch removal makes middlings an excellent low‐energy addition to diets for gamebirds for release. Although the (estimated) amino acid needs of gamebirds can be met with the use of vegetable proteins and pure amino acids, most nutritionists include animal protein products like meat and bone meal or fish meal to achieve a better amino acid balance, and to reduce the amount of soy NSP (especially in starter diets). Although good‐quality fish meal has become expensive and hard to source, and bovine meat and bone meal is avoided due to the threat of bovine spongiform encephalopathy (BSE), porcine meat and bone meal are still readily available. In addition to the protein, meat and bone meals are a good source of phosphorus that often provide an economic advantage. Disadvantages include inconsistent levels of calcium and phosphorus and the potential presence of pathogens if not processed properly. Fats and oils can be a major source of energy in feed, due to their content of an average of 2.5 times as much energy as that in grains. However, the extra energy is only needed in high‐energy meat bird diets (and some breeder diets), while birds for release should be provided lower energy levels to perform well. Although added fat is helpful for controlling dustiness and improving palatability in mash diets, its use in pelleted diets must be limited to a maximum of approximately 2% because of the negative effect it has on pellet quality. Fats and oils are made up of a glycerol molecule with three attached side chains of fatty acids usually containing 8–24 carbon atoms. The carbons are linked by single or double bonds indicating saturation or unsaturation. Fat is solid at ambient temperatures (more single bonds, or saturation), whereas oils are liquid (more double bonds). Evaluation of quality is based on features such as color, fatty acid profile and saturation or unsaturation, the percentage of free fatty acids, and MIU (moisture, insolubles, unsaponifiables). For feed fat, color is not as important as it is in human or pet food, but it may be an indicator of abuse in processing. Fatty acid profile depends on the source, with animal fats trending toward more saturation while vegetable oils usually contain more unsaturated fatty acids, which are more digestible for poultry. Free fatty acids are those that have separated from the glycerol molecule, and high percentages may indicate oxidative damage. The higher quality feed fats contain no more than 10% free fatty acids. Feed fat should contain no more than 1.5% moisture, 0.5% insolubles (like fiber, hair, minerals) and a maximum of 1% unsaponifiables (like sterols, pigments) if from animal fat, or 4% if from vegetable oil. The ideal MIU maximum would be 2–2.5%. A standard fat testing protocol (especially fat from a new supplier) should also include scanning for PCBs and pesticides. Finally, antioxidants like ethoxiquine, BHT (butylated hydroxytoluene) or BHA (butylated hydroxyanisole) should be added to all fats to prevent oxidation and rancidity. Definitions of all approved nutritional and nonnutritional products are listed in the Association of American Feed Control Officials (AAFCO) (2021) [3] but only minimal additional information is included. The American Feed Industry Association (AFIA) Feed Ingredient Guide (1995) [4], although out of print, contains information that is hard to find elsewhere, including factors that influence quality, availability, physical properties, and major feed applications. Manufacturers or distributors of ingredients provide specification sheets detailing the composition of their product. This information is essential for accurate formulation. As with grains, proteins, and fats, all ingredients from an unproven supplier should be tested independently to confirm that they meet specifications. Molds are always present, averaging 500 000 cfu/g while levels above 1 million cfu/g are considered of concern. Mold itself is usually not dangerous. In high‐moisture conditions, it grows, digests feed, and reduces the feed’s value to the bird. However, under suitable conditions, molds produce mycotoxins which can be very dangerous to gamebirds. At times when feed may be stored for too long (more than 3–4 weeks) or there is the increased possibility of water condensation due to temperature fluctuations (spring or fall seasons), a mold inhibitor is highly recommended. Pheasants, ducks, and turkey poults are quite sensitive to the effects of mycotoxins. Aflatoxins can cause reduced performance when present in the 10–20 parts per billion (ppb) range. Many other common mycotoxins like T‐2 or fumonisins are dangerous in the parts per million (ppm) range, cause liver and kidney damage, and are to be avoided when possible. The most common symptoms reported are lesions in the mouth and throat; poor eggshell quality in layers and breeders; and stunting, poor growth, and rickets in growing birds as a result of liver, kidney, and intestinal damage. In other livestock, feed refusal, poor growth performance, and poor reproductive performance are observed. Almost every year, weather conditions cause stress on the corn and other crops. That stress increases the potential for mold growth before harvest. Inadequate storage of the previous year’s crop also leads to after‐harvest mold growth during storage. It is common to see more than one type of mold or mycotoxin in a sample and toxicity may be from multiple sources. Areas where feed manufacturers can reduce problems include ingredient storage and preparation, feed manufacturing changes, use of additives and nutrition‐related changes to reduce or overcome symptoms. These measures will prevent or reduce mold growth, but will not affect mycotoxins that are already present.
7
Gamebird Nutrition
7.1 Feed Type
7.1.1 Suggested Nutrient Levels
Nutrientb) – %, IU/lb, mg/lb
Starter
Starter #2
Growerc) (meat)
Flyer (finisher)
Maint‐enanced)
Breedere) (small)
Protein %
26–28
23–24
20 (22)
18 (20)
14–16
18–20 (23–24)
ME kcal/lb
1250
1250 (1318)
1250 (1318)
1200 (1350)
1150 (1250)
1273 (1300)
Calcium %
1.25
1
1
0.75
0.7
2.5 (2.6)f)
Phosphorus (avail.) %
0.65
0.5
0.5
0.4
0.4
0.55
Sodium %
0.16
0.16
0.16
0.16
0.16
0.16
Chloride %
0.15
0.15
0.15
0.15
0.15
0.15
Met + Cys %
1.1
0.95
0.8 (0.85)
0.6 (0.75)
0.6
0.75
Lysine %
1.65
1.4
0.95 (1)
0.8 (1.0)
0.75
0.95
Threonine %
1.1
1.05
1
1
0.7
0.75
Tryptophan %
0.26
0.25
0.25
0.25
0.18
0.2
Vitamin A (IU)
6000
6000
5100
4800
4200
6500
Vitamin D (IU)
2500
2500
2125
2000
1750
3000
Vitamin E (IU)
40
30
20
20
10
50
Vitamin K (mg)
2.2
2
1.8
1.7
1.5
2.2
Thiamine (mg)
3
3
3
2
2
3
Riboflavin (mg)
7
5
4
4
3
7
Pantothenic acid (mg)
15
15
12
12
10
15
Niacin (mg)
70
60
40
40
30
75
Folic acid (mg)
3
3
2.55
2.4
2.1
2
Pyridoxine (mg)
5
5
4.25
4
3.5
5
Choline (mg)
900
900
765
720
630
900
Vitamin B12 (mg)
0.03
0.03
0.03
0.024
0.02
0.03
Biotin (mg)
0.3
0.3
0.255
0.24
0.2
0.3
Iodine (mg)
1.5
1.4
1.3
1.2
1.05
0.5
Manganese (mg)
70
60
60
50
40
60
Copper (mg)
15
10
10
10
10
15
Iron (mg)
60
50
50
50
40
50
Zinc (mg)
100
80
80
80
40
100
Selenium (mg)
0.13
0.13
0.13
0.13
0.13
0.13
7.2 Feed Ingredients
7.2.1 Ingredient Quality
7.2.2 Corn (Maize)
7.2.3 Soybeans and Soybean Meal
7.2.4 Wheat and Wheat Middlings
7.2.5 Meat Products (i.e., Meat and Bone Meal, Fish Meal)
7.2.6 Fat, Oil
7.2.7 Minerals, Vitamins, Amino Acids, and Nonnutritional Ingredients
7.3 Mold Control
7.3.1 Controlling Mold Growth in Ingredients
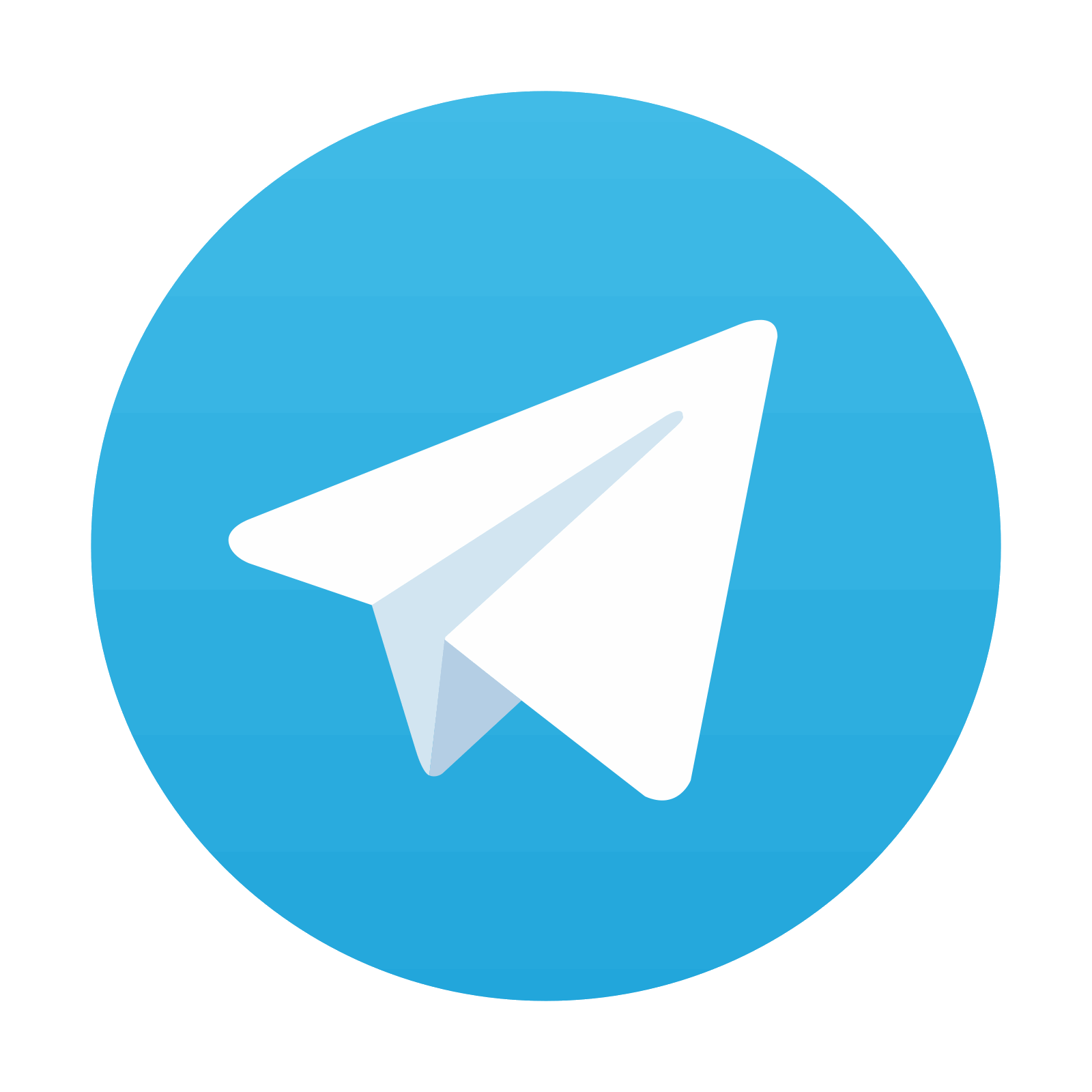
Stay updated, free articles. Join our Telegram channel
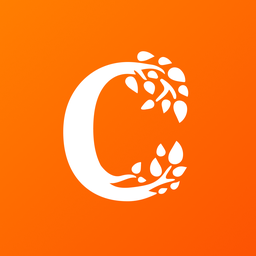
Full access? Get Clinical Tree
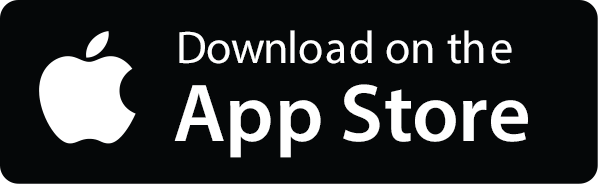
